Move goods efficiently and quickly with conveyors
Manufacturers, warehouses, and distribution centers know the supply chain is simply people and technology working together to move goods. Nearly everything we use on a daily basis was manufactured, distributed and sold, whether to a box store, an OEM, or directly to a consumer. Conveying equipment kept those goods moving, allowing them to get where they were needed as fast as possible.
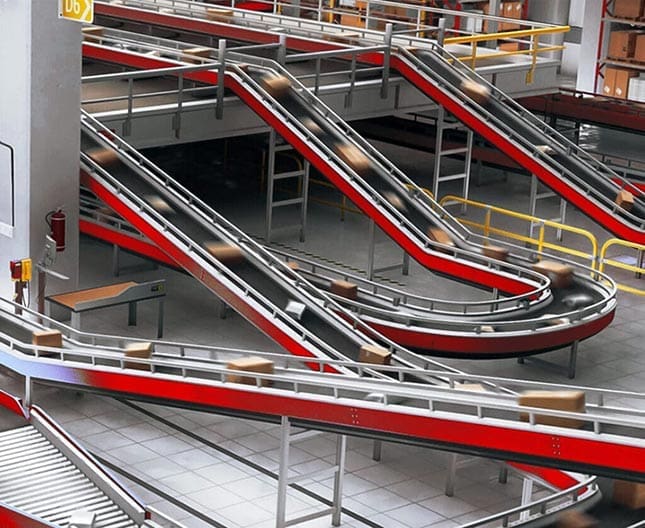
Bottlenecks in material handling means falling behind
Whether you’re manufacturing car parts or fulfilling ecommerce orders, consumers want a wider variety of products produced and shipped faster than ever. Material handling operations need to be nimble to meet just-in-time delivery expectations and ecommerce orders of increasing complexity. If your operation relies on manual picking, or if you’re using outdated conveyor technology that simply moves goods from one place to another, you’re adding bottlenecks that slow you down instead of automation that speeds you up.
Automated conveyor systems let you do more
Warehouse conveyor systems increase throughput at every stage of your operation. From transportation to sorting, loading to unloading, and order fulfillment to quality control, conveyors automate otherwise manual work. They get goods where they need to go on time, integrating with existing systems, including your WCS/WMS. Every operation is different, but all can do more with the right conveyors.
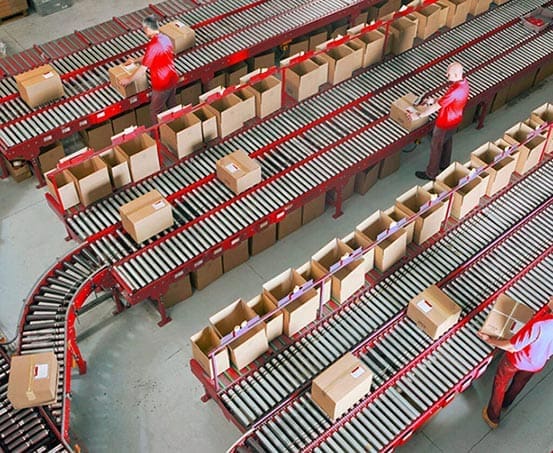
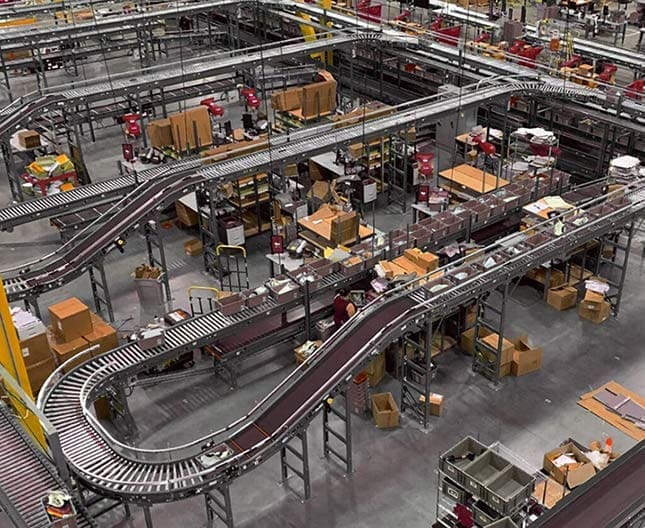
Reliability and efficiency without having to hire
Receivers, pickers, inventory managers, forklift operators, and more. Automated conveyor systems increase the efficiency of the roles in your operation. Set simple rules in your WCS/WMS software to intelligently route orders via conveyors to the right station for picking or packing, or to move parts between product lines. With conveyor systems designed for your exact needs, you’ll get reliable, repeatable success while reducing labor cost and complexity.
Safer manufacturing with material handling conveyors
Moving goods around the floor of a plant is demanding, and mistakes can cause injuries. Automated conveyor systems take on straining, repetitive work, moving product into inventory, through production lines, and finished goods through quality control and shipping. Conveyors protect the efficiency, ergonomics, and overall safety of your plant.
Fully integrated conveyor systems. We help manufacturers get the most of their systems through autonomous solutions that work together. Those include:
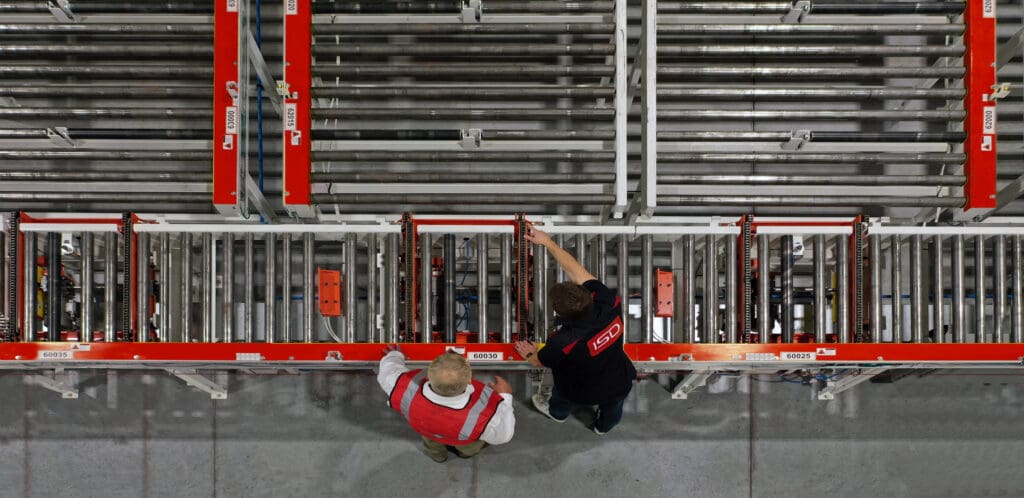

Pallet conveyors
Live roller: a large roller conveyor, like a parcel conveyor, but designed to handle pallets. It’s used for longer run distances with consistent, quality pallets or trays.
Drag chain: a chain system where the pallets or trays ride on a conveyor. This type of system is used where there are lots of diverts required or the quality of the pallets or trays may not be good enough for a live roller type of system. It’s used heavily in manufacturing with many work cells.
Pallet transfers: a diverter or sorter for pallets for both live roller and chain conveyors.

Automated Systems
Automated trailer loading systems. These conveyors plug into your operation’s shipping system, extending in-plant conveyors into over-the-road LTL trailers, as well as conveyor-friendly vans from carriers.
Automated assembly lines. We design custom conveyors for every part of your build or assembly lines, including transferring inventory and tools to and from work stations.
Autonomous guided vehicles (AGVs) and automated guided carts (AGCs). Mobile robots transport materials while working in tandem with conveyors to keep production lines running. They operate continuously and safely, reducing material handling accidents or bottlenecks in your operation.
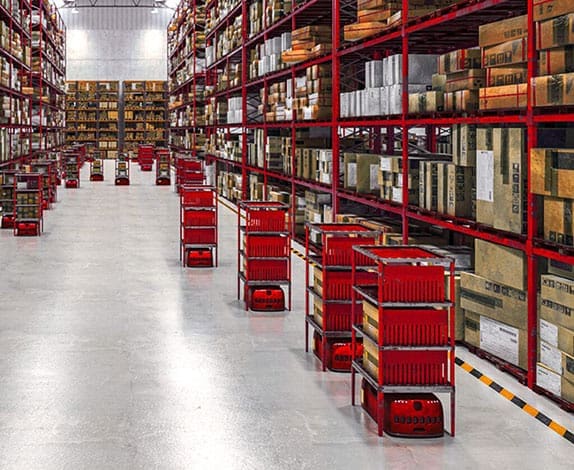
Automate for Safer Jobs
Equipped with safety laser and camera sensors, AGVs and conveyors moving heavy pallets around your floor in programmable paths decrease the risk of forklift accidents or worker injuries from manually moving materials. Let automation take on the repetitive tasks, and free up you and your team to continue improving operations and oversee quality.
Is your existing transport system designed to make the most of your automation investments, while keeping your workers safe and your uptime high? ISD designs top-down solutions for the modern plant to ensure automation brings you the highest, fastest ROI possible.
Is your existing transport system designed to make the most of your automation investments, while keeping your workers safe and your uptime high?
ISD designs top-down solutions for the modern plant to ensure automation brings you the highest, fastest ROI possible.
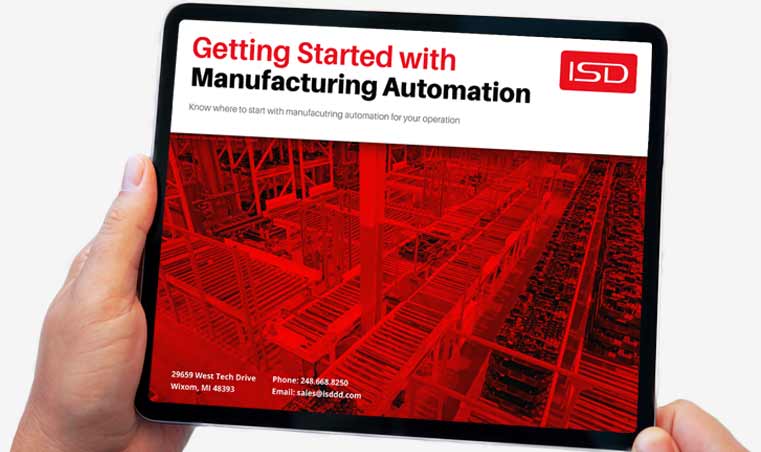

Not sure where to start with automating your warehouse?
Take the first step and download our eBook to get your questions answered.
Download the eBook
Keep your distribution center on track with conveyors
What happens in the warehouse can make or break your business. When a sale comes in, you have limited time to pick, pack, and ship it correctly — or risk that customer not ordering again. Automation fulfills orders accurately, and conveyors get goods where they need to be in a fast, safe, and repeatable way. Streamline your operation with modular conveyor solutions tailored to your warehouse.
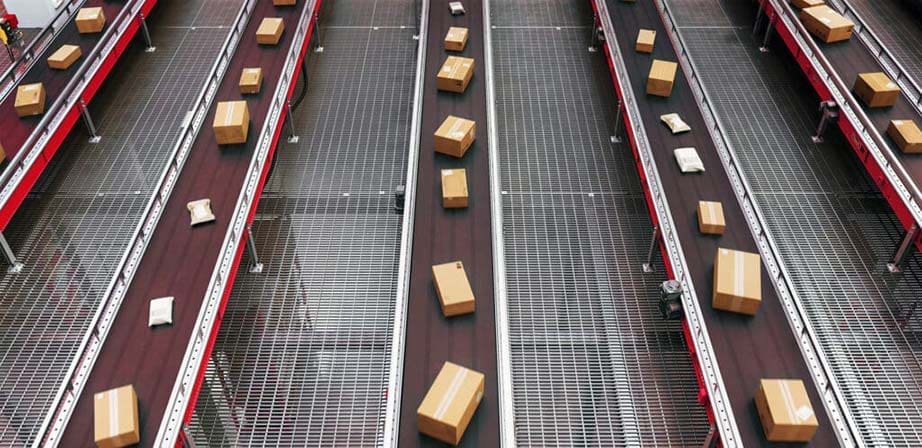

Merge & Pallet conveyors
Belt merge: a high-speed merge for up to four lanes into a single lane using plow arms to merge product.
Sawtooth merge: combines many lanes of conveyor onto a single conveyor at high speed.
Live roller merge: a cost effective way of merging several lanes into a single lane when lower volumes are required.
Live roller: a large roller conveyor, like a parcel conveyor, but designed to handle pallets. It’s used for longer run distances with consistent, quality pallets or trays.
Drag chain: a chain system where the pallets or trays ride on a conveyor. This type of system is used where there are lots of diverts required or the quality of the pallets or trays may not be good enough for a live roller type of system.
Pallet transfers: they work as a diverter or sorter for pallets for both live roller and chain conveyors.

Sortation systems
Narrow belt sorters: high-speed conveyor where products run on belts and sort at very high speeds, typically for parcels or totes.
Cross belt sorters: high-speed sortation of envelopes and packages or totes for easy sortation in a smaller footprint. Great for hard-to-sort parcels and sorting individual products.
Shoe sorters: high-speed sorter that handles large volumes of product at high speeds, but offers a much wider range of size and weight capabilities. It typically handles parcels and cases.
Tilt tray sorters: typically a self-contained system offering high-speed sortation of products that are almost impossible to sort by other systems. This might include jewelry, soft goods, or media. This system is usually used to sort individual products into orders.
Push sorters: much like a tilt tray sorter, the push sorter uses a “push” arm to sort products into orders. These can be very large systems with hundreds of sort lanes. However, this type of sorter can handle a wider range of product and parcel types and sizes.
Robotic sorters: these robots actually sort. Multiple robots work to sort products into orders, just as a tilt tray sorter does. In fact, many of these robots “tilt” to deliver products to their sort destination.

Accumulation conveyors
Zero pressure accumulation conveyor: allows for sequenced, high-speed movement of totes and cartons with zero contact between conveyed items. This enables the conveyor to tightly control the flow and allows for sortation, routing, and automated processing of products.
Low or medium pressure accumulation conveyor: allows for cartons or totes to accumulate together with little pressure. This is ideal for getting the most density on a conveyor system while still controlling product movement.
Custom accumulation conveyor: at times, accumulation of products needs something unique or specialized. ISD can develop custom accumulation conveyor solutions for your operations’ specific needs.

Other conveyor systems
Belt, roller, pallet, and portable conveyors. Conveyors can be made from various materials to serve a variety of use cases. In a fulfillment setting, conveyors can be used to transport materials, accumulate orders, buffer orders, and sequence picks and orders for shipping.
Vertical and reciprocating lifts or spiral conveyors. Used to move products vertically, typically used for moving parcels or totes to and from different levels (like from mezzanine to multiple stories). Vertical lifts work like high-speed elevators, whereas a spiral is typically a belt conveyor that products or parcels ride on. Vertical lifts are slower than spirals, but have the ability to handle larger and heavier products.
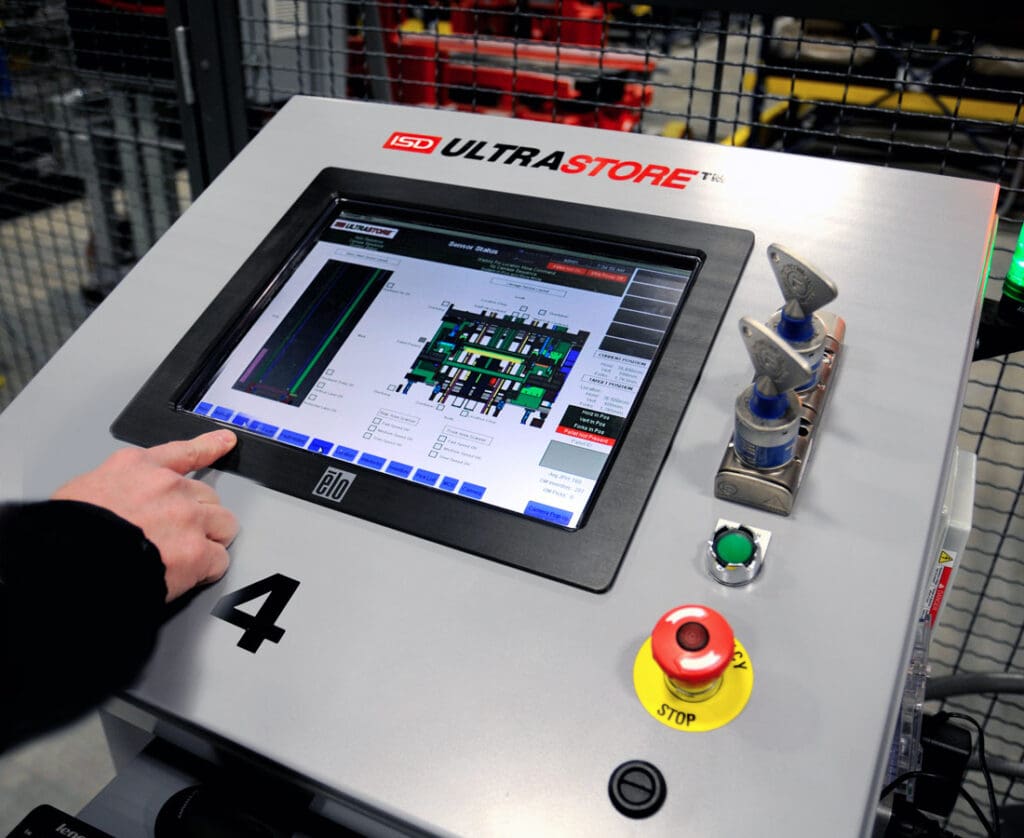
Conveyors that are easy for everyone to operate
Conveyors can be coded with software that integrates with an existing WMS/WCS to automate order processing. For instance, when a new tote is placed on a conveyor system in a warehouse, a barcode on that tote is tagged to the order that’s being picked into it. As it travels along the conveyor, the system controls each tote, directing it to the picking locations for the item the order contains. Your team can oversee the process, but the hardware and the software process the work.
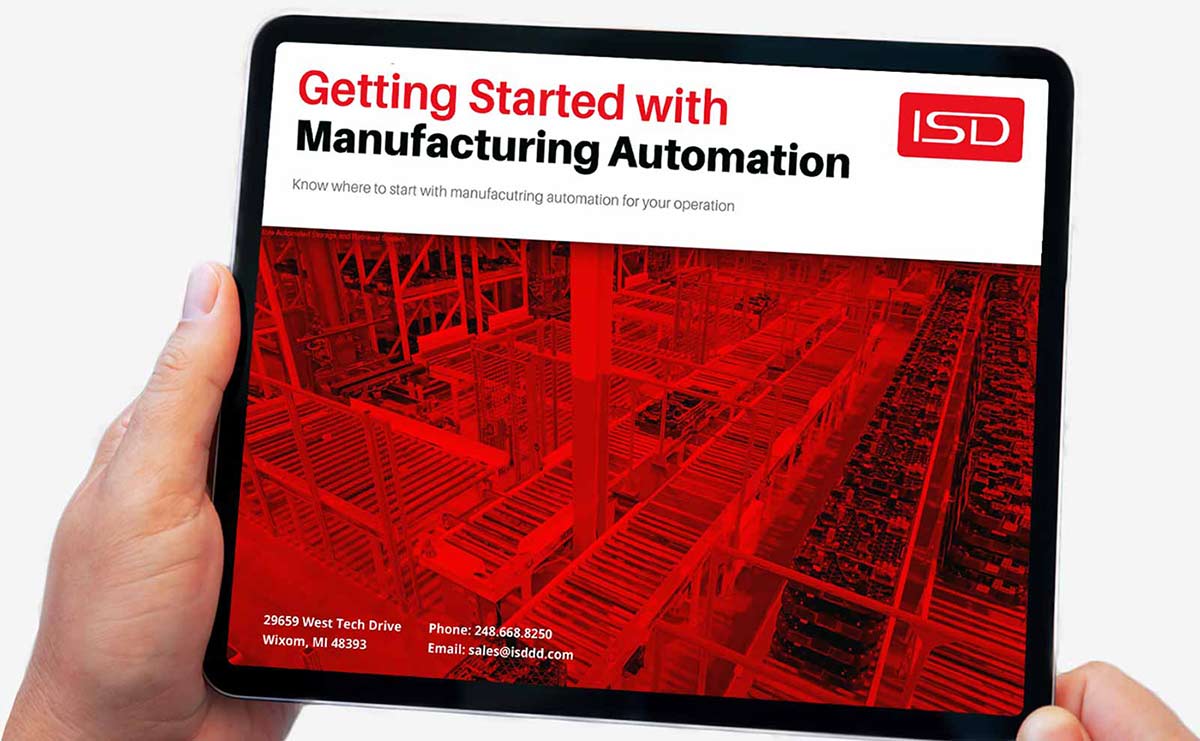

Learn how to automate your manufacturing operation.
Take the first step and download our eBook to get your questions answered.
Download the eBook
Related Resources
Related Solutions
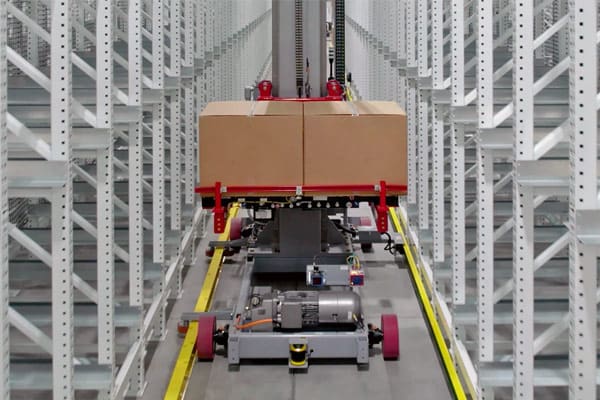
Automated Storage & Retrieval
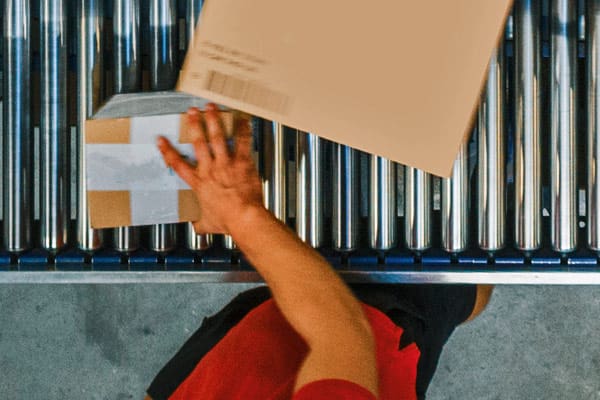
Order Picking & Fulfillment
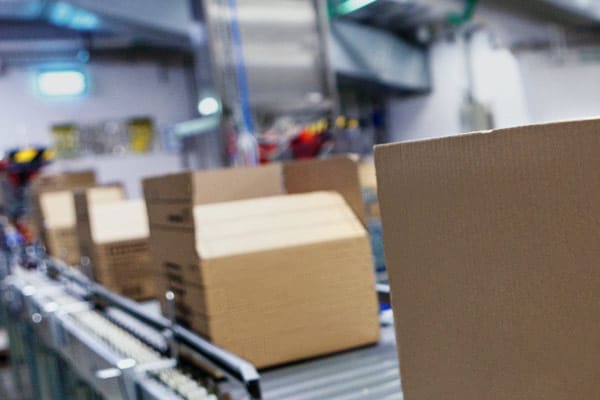
Packing Systems
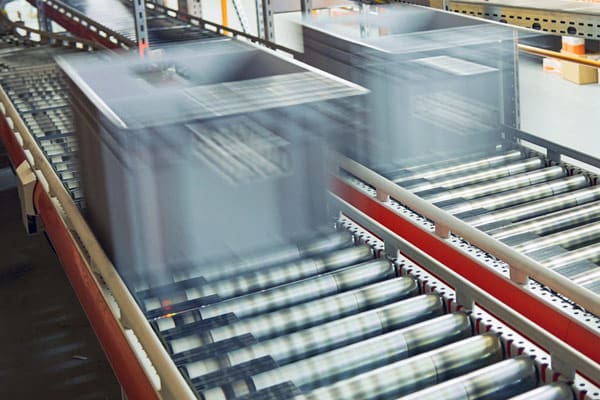
Shipping Systems
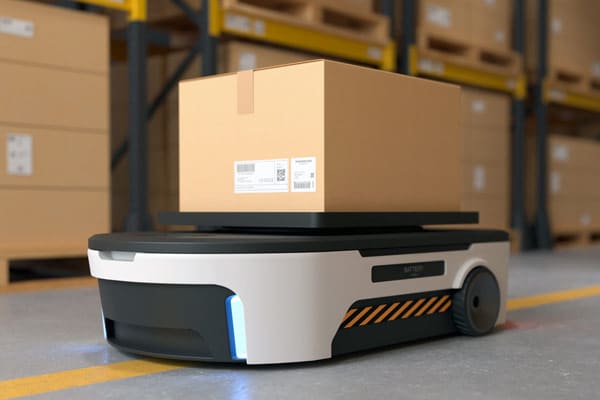
Robotics
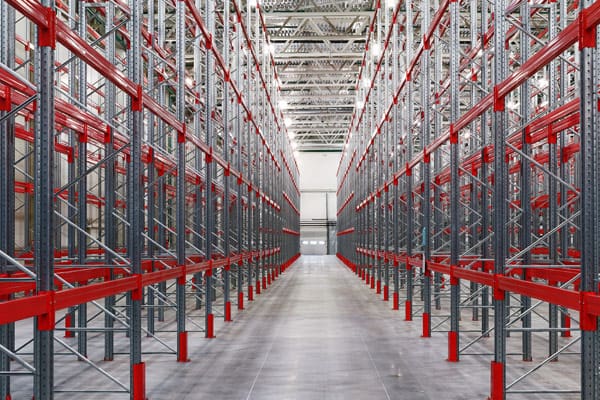
Storage
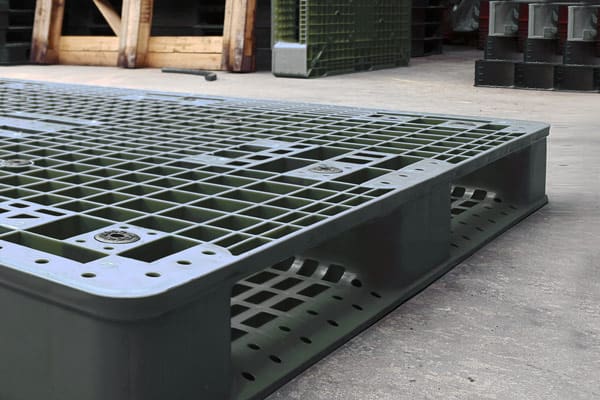
Pallet Management
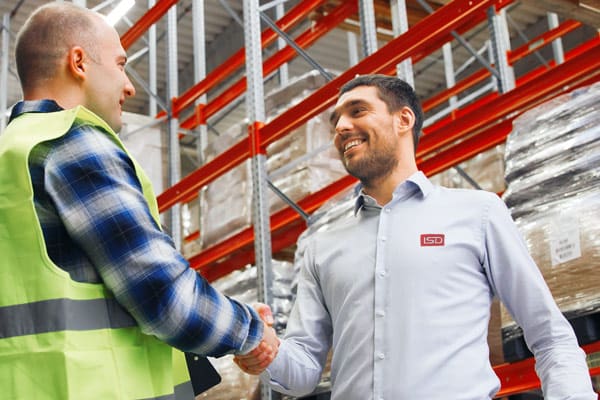
Talk with an Automation Expert
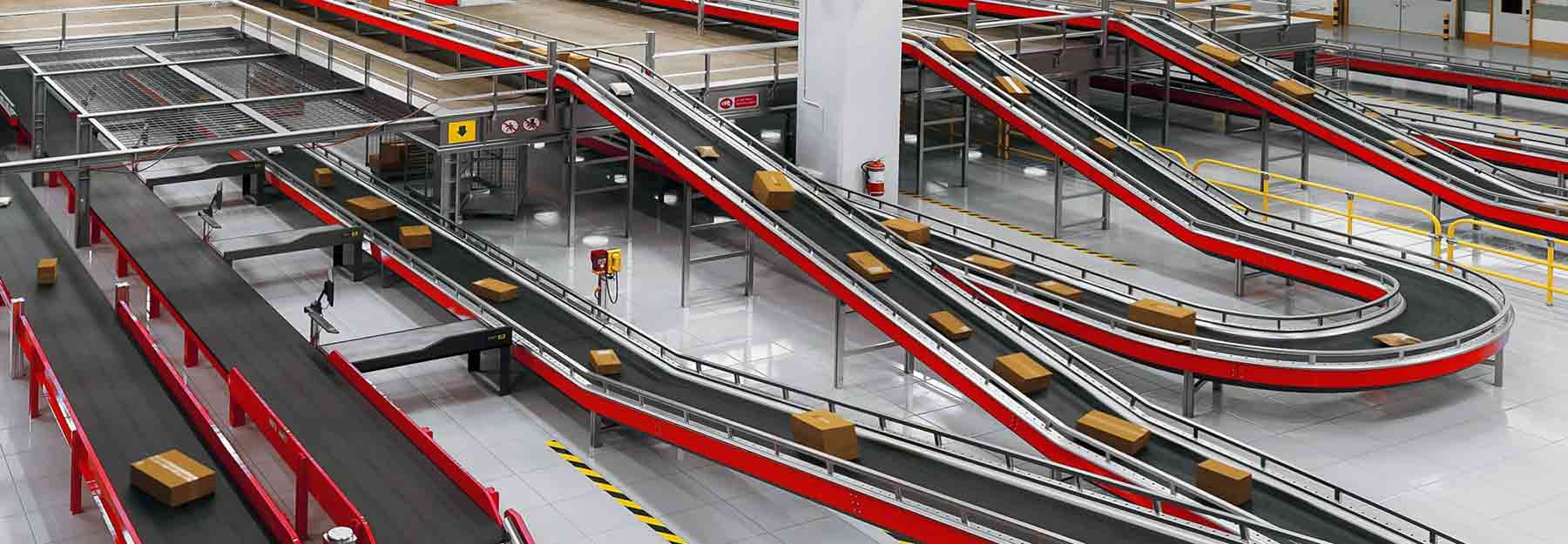
Custom conveyors, streamlined solutions.
You’ve got a lot to convey. Exceed your customer’s expectations with reliable, repeatable systems that take care of their order requirements. Conveyor systems increase productivity while keeping your workers safe and your fulfillment time down. Where could a conveyor help streamline your operations?